System Status | Problem | Solution(s) |
PAPERPATH_FEED_TIME OUT | - Out of Paper
- Media is not reaching the print engine.
- Hesitation in media feed.
| - Load media into printer and press the PAPER/RESUME button. If media is present; check/adjust the guides and separators. Tip: It is also possible to get this error if the media jams after reaching the Paperpath Exit sensor, and the trailing edge is still in the Entry sensor. See below
|
- Possible Paper Jam; if error is shown in combination with “Reason: Uncapped printhead or clamshell open” message.
- Problem with Paperpath Entry Sensor or paper sensor in feed section.
| 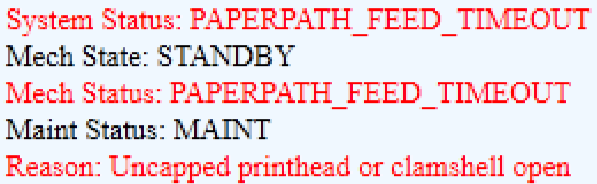 - See “Paperpath_Paperjam” solutions.
- Check/clean sensors.
- Call for service.
|
- Purge Bar Position (BoF) is exceeding gap between pieces and confusing printer.
| - Reduce purge bar position setting. Should be set, so it purges, 3mm past edge of media. Check value in Toolbox and Driver. Values are cumulative.
|
PAPERPATH_PAPERJAM Paperpath: Entry:Yes Exit:Yes or Paperpath: Entry:No Exit:Yes or Paperpath: Entry:Yes Exit:No No = not blocked Yes = blocked (interrupted)
| - Paper Jam Media jam detected.
- Printer has detected that one of the media sensors is blocked (interrupted)
| - Carefully open the Clamshell, remove jammed Media from printer and close the Clamshell. The System Status message in red should go away. The toolbox “Paperpath” line should change to: Paperpath: Entry: No Exit: No
- If not; sensors may need to be cleaned.
- After you clear the jam you can:
- Press RESUME button to continue printing.
- Press the CANCEL button to cancel the job, and then manually clear the job from the computer’s print queue.
|
PAPERPATH_PAGE_SEQUENCE | - Paper length change detected.
- Paper density change detected. In this case the error may change to Paperpath_Paperjam shortly after detection.
|
|
X_INK_LOW Example: CYAN_ INK_LOW
| X = Color. One or more Ink Tanks are low on ink. | - Ink Tank replacement will be necessary soon.
|
INK_OUT_X Example: INK_OUT_YELLOW 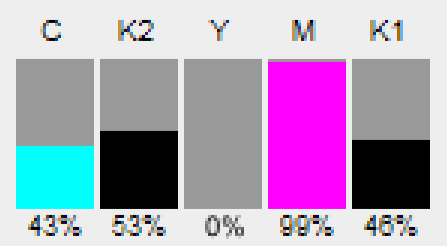
| X = Color or MULTI One or more Ink Tanks are out of ink NOTE: If the message “INK_OUT_ANY” is displayed; please contact service support and ask them to update the printer’s firmware.
| WARNING! Use proper procedure to replace Ink Tank(s) to avoid damage. - Select “Replace Ink Tanks”, then verify that Ink Tanks are seated firmly and latches are fully closed.
- Verify that the printer is on a stable, level surface. Try to clear the error by pressing the “Refresh Ink Levels” button, located in the Toolbox.
|
CARTRIDGE_MISSING_X
| X = Color or MULTI Missing Ink Tank, or Ink Tank not being recognized | |
DOOROPEN_FRONT | - Printer has detected that the “Clamshell” is open.
| - Verify that the “Clamshell” is closed and securely latched at both sides.
- If closed; contact Service to check latch & switch
|
MAINTENANCE_BUSY | - Printer is performing maintenance.
| - No action is required. Wait for printer to finish.
|
- Printer is waiting to perform maintenance;
- If error is shown in combination with“Reason: Uncapped printhead or clamshell open"and there is no maintenance activity (noise) coming from printer.
| - Remove media from print engine. See “Paperpath_Paperjam” solutions.
- If problem continues clean Paperpath Entry and Exit sensors. NOTE: Selecting “Ignore Exit Sensor”, in the Toolbox, will not solve issues caused by a non-responsive Exit Sensor.
- If problem continues contact Service.
|
System Status: ONLINE Reason: Uncapped printhead or clamshell open
| - This condition will be displayed after the Service Station is ejected (using the Eject Service Station button).
| |
DATA_PATH_UNDERRUN | - Media is not making it from the entry sensor to the exit sensor in the appropriated time.
- Possible issue with format or orientation of job being sent.
- Dirty Encoder Wheel
| - Check/clean transport rollers.
- Check/clean sensors.
- Try changing the orientation setting in the software/driver or setting a different media size.
- Check/clean the Encoder Wheel.
- If problem persists contact technical support.
|
[Crit 63 03-phead offline cancelpage restart] | - Dirty Printhead contacts.
- Printhead or Pen Board fault.
| - Eject Printhead and inspect/clean contacts.
- Replace Printhead.
- Call for Service Support.
|
PRINTHEAD_MISSING | - Printer is still initializing or some other issue is keeping it from fully initializing.
| - If printer was just powered on, or printhead was just installed; wait a few minutes, error should clear by itself.
- Call for Service Support.
|
PRINTHEAD_MISSINGQA | - No printhead installed or printhead not making proper connections.
| - Install Printhead Cartridge.
- Remove Printhead and check/clean contacts; then reinstall Printhead.
- Replace Printhead.
|
PRINTHEAD_UNPRIMED | - Printhead priming process has not complete or has failed.
- Ink delivery issue.
| |
MECH_CANCELPAGE | - Job was canceled by user pressing the CANCEL button.
- Job was interrupted by “Clamshell” being momentarily opened.
| - Wait until print job has cleared from printer. Then manually clear job from computer’s print queue. Then send new print job. Check to be sure “Clamshell” is securely latched, and then press “Clear Error” button to continue.
- If problem continues contact service support.
|
MECH_FAIL_PERMANENT Reason: Sled lift failed Reason: Ink valve failed Reason: Sled home failed
| - Mechanical failure or sensor failure.
- One of the printer’s mechanical components was not properly registered at the expected position.
| - If the Service Station was just installed; check to be sure it was installed properly.
- If problem persists, call for Service Support.
|
WIPER OVERTEMP
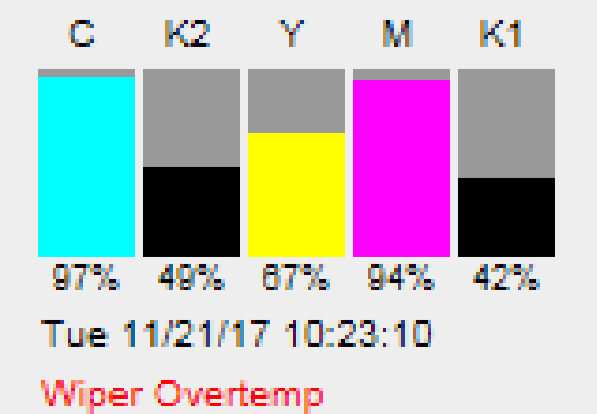 | - Wiper Motor is overheated due to performing a Wiper Transfer (removing excess ink off Service Station Wiper) too often or for multiple or extended periods. Printer will continue maintenance after Wiper Motor cools down. Message will disappear once the temperature returns to operating range.
| - Wait for Wiper Motor to cool down, Printer will automatically resume operation. NOTE: If running a number of short jobs or jobs on smaller media, reset Mid-Job Servicing interval to a higher number of pages.
|
WIPER ERROR
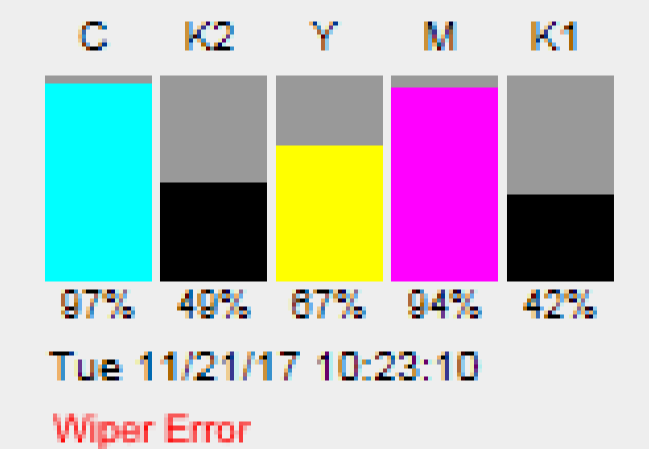 | - Wiper Roller is too hard to turn, due to coagulated ink.
- Wiper Roller is not turning.
| - Run “Wiper Preemptive Maintenance” routine.
- Check white flex cable connection to Service Station.
- Replace Wiper Motor Module or Service Station.
- If problem persists, call for Service Support.
|